Octet Design PD1
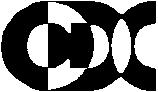 |
©1998 Octet Design Corporation
|
8-18-98
|
|
PD1 Manual
|
|
PACKING LIST
PD1 driver board.
6 ft data cable.
8 DB-25 female solder.
Software disk.
This manual.
optional
AD-9 power supply
Optical switch assembly
Stepper motor
DESCRIPTION
The PD1 is a driver board for perforating machines.
It interfaces to the PC's printer port, it is compatible with Wayne
Stahnke's Punch software.
INSTALLATION
Plug in the data cable from the computer's printer port to the PD1.
Jumpers:
JP2 |
ON = connects solenoid power to logic power (25 volts max)
OFF = default, logic power is separate |
JP3 |
ON = connects stepper motor power to logic power (25 volts max)
OFF = default, logic power is separate |
JP4 |
ON = connects the motor outputs (122-125) catch diodes to the motor
power
OFF = if outputs are unused or if motor connected |
JP5 |
TIMEOUT = output 126 is timeout output (may be permanently soldered)
NORMAL = output 126 is normal |
JP6 |
Base address selector: from left = addr 0, addr 128, addr 256,
addr 384 |
JP 10 |
Polarity of TRIG1: left = negative, right = positive, no jumper
= inactive |
JP 11 |
Polarity of TRIG2: left = negative, right == positive, no jumper
= inactive |
JP 12 |
MAIN = main duty cycle control to outputs 120-127
MOT = stepper motor duty cycle control to outputs 120-127 |
JP 13 |
DOWN, do not change |
Potentiometers:
MAIN |
adjusts solenoid's duty cycle. Set to 25% at factory. |
ST. MOT. |
adjusts stepper motor's duty cycle. Set to 25% at factory. |
OSC |
adjusts oscillator frequency. Set to 25 KHz at factory. |
TIMEOUT |
adjusts timeout to pin 126 |
SPECIFICATIONS
|
Minimum |
Maximum |
Logic voltage |
9 volts |
25 volts |
Solenoid voltage |
|
50 volts |
Stepper motor voltage |
|
25 volts |
Output current - continuous |
|
2 amps |
Output current - 50% duty cycle |
|
4 amps |
Output current - 25% duty cycle |
|
8 amps |
Power relay current |
|
5 amps |
Power relay voltage |
|
240 volts AC |
CONNECTORS PINOUTS
TRIG1 and TRIG2:
Pin
1 Ground
2 Emitter supply (180 ohms to 5 volts)
3 Ground
4 Sensor output (4.7 kohms to 5 volts)
Stepper Motor connector J3:
Pin
1 Phase D
2 Step motor positive
3 Phase B
4 Step motor positive
5 Phase C
6 Step motor positive
7 Phase A
8 Step motor positive
Stepper Motor power connector J6:
Pin
1 Step motor positive
2 negative
3 negative
4 Step motor positive
Output connectors: DB-25 connectors for outputs.
Pin |
Output |
Output |
Output |
Output |
Output |
Output |
Output |
Output |
1 |
0 |
16 |
32 |
48 |
64 |
80 |
96 |
112 |
2 |
positive |
positive |
positive |
positive |
positive |
positive |
positive |
positive |
3 |
negative |
negative |
negative |
negative |
negative |
negative |
negative |
negative |
4 |
4 |
20 |
36 |
52 |
68 |
84 |
100 |
116 |
5 |
positive |
positive |
positive |
positive |
positive |
positive |
positive |
positive |
6 |
negative |
negative |
negative |
negative |
negative |
negative |
negative |
negative |
7 |
8 |
24 |
40 |
56 |
72 |
88 |
104 |
120 |
8 |
positive |
positive |
positive |
positive |
positive |
positive |
positive |
positive |
9 |
negative |
negative |
negative |
negative |
negative |
negative |
negative |
negative |
10 |
12 |
28 |
44 |
60 |
76 |
92 |
108 |
124-mot. |
11 |
positive |
positive |
positive |
positive |
positive |
positive |
positive |
positive |
12 |
negative |
negative |
negative |
negative |
negative |
negative |
negative |
negative |
13 |
NC |
NC |
NC |
NC |
NC |
NC |
NC |
NC |
14 |
1 |
17 |
33 |
49 |
65 |
81 |
97 |
113 |
15 |
2 |
18 |
34 |
50 |
66 |
82 . |
98 |
114 |
16 |
3 |
19 |
35 |
51 |
67 |
83 |
99 |
115 |
17 |
5 |
21 |
37 |
53 |
69 |
85 |
101 |
117 |
18 |
6 |
22 |
38 |
54 |
70 |
86 |
102 |
118 |
19 |
7 |
23 |
39 |
55 |
71 |
87 |
103 |
119 |
20 |
9 |
25 |
41 |
57 |
73 |
89 |
105 |
121 |
21 |
10 |
26 |
42 |
58 |
74 |
90 |
106 |
122-mot. |
22 |
11 |
27 |
43 |
59 |
75 |
91 |
107 |
123-mot. |
23 |
13 |
29 |
45 |
61 |
77 |
93 |
109 |
125-mot. |
24 |
14 |
30 |
46 |
62 |
78 |
94 |
110 |
126 |
25 |
15 |
31 |
47 |
63 |
79 |
95 |
111 |
127 |
Note: outputs 122-125 are also available on the stepper motor connector
Printer connector: DB-25
1 STROBE - active low to enable data output
2 ADDRESS 0 - address of output
3 ADDRESS 1 - address of output
4 ADDRESS 2 - address of output
5 ADDRESS 3 - address of output
6 ADDRESS 4 - address of output
7 ADDRESS 5 - address of output
8 ADDRESS 6 - address of output
9 ADDRESS 7 - address of output
10 TRIG2 - trigger input
11 Ground
12 TRJGI - trigger input
13 No connection
14 DATA - data bit to output
15 DIAG - data in
16 DUTY - duty cycle control: 1 = 100%, 0 =
25%
17 ADDRESS 8 - address of output
18-25 Ground
PROGRAMMING
DATA OUTPUT:
To output a bit of data to a certain output, place the address of this
output on the 8 ADDRESS
lines and the data on the DATA line. Then strobe the STROBE line.
Aii signals at the connector are active low. Some signals, however
are inverted at the printer chip
in the PC, so the resulting polarity of the control bits:
Address 0 to 7: inverted
Address 8: straight
Data: straight
Strobe: inverted, write a 1 then a 0.
Note: The outputs are active low, so a data 1 means a low output. All
outputs are reset at power
up. There are 9 address bits because the address range of the board
is selectable.
DIAG INPUT:
To read the status of an output, read DIAG during the strobe period.
It is valid only during the
strobe active period, for the selected address.
DUTY CYCLE CONTROL:
There are two duty cycle oscillators. The main one affects all outputs
or all except motor outputs
(120-127), depending on jumper JP12. The motor duty cycle affects outputs
120-127 or none
depending on jumper JP12.
The main duty cycle is controlled by the line DUTY, 1 = 100%, 0 = 25%.
The motor duty cycle is controlled by output 126, 2 = 100%, 0 = 25%.
Note: The purpose of controlled duty cycle in this case is to pull
the solenoids at full power and
then immediately cut down the power by reducing the duty cycle.
POWER RELAY:
The power relay is controlled by output 127. Its use is optional.
TIMEOUT FEATURE
If enabled by jumper JP5, output 126 is meant to control a relay, which
turns on when strobe is
active, and turns off a few seconds after strobe activity stops. The
delay is adjustable. The relay
can be used to control power to the solenoids, to avoid damage in case
the PC crashes.
19 December 2000
|